Furnace Charger
We are leading Furnace Charger, Manufacturers, Suppliers and Exporters Located in Ambarnath MIDC Dist Thane, Maharshtra India.
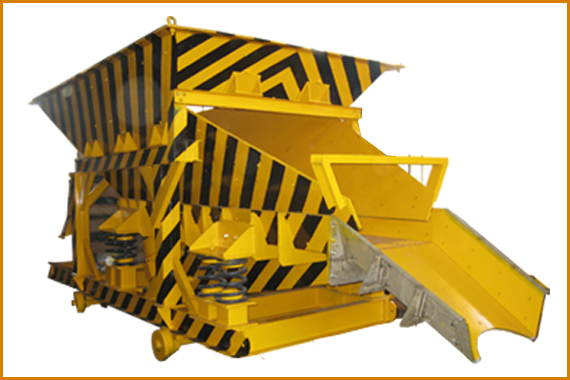
High quality foundry products are in huge demand nowadays. The cost effective production of these products places high demands of the charging equipment for melting plants. Though much of the production in foundries is achieved by automation, i.e. melt shop automation. It includes remote furnace charging systems. Let us have below the brief about induction furnaces & remote furnaces.
Induction furnaces:
Today’s most technologically advanced induction furnaces provide high power densities & are able to run to full power throughout the charging process. It is important to keep pace with the melting power of the system, which requires rapid furnace charging. However, charging the furnace can be a labor intensive, manual & time consuming operation.Charge materials are simply dumped into the furnace with wheel barrows or dropped inside manually. Besides, the inefficient use of manpower & time, manual operation can damage the furnace linings, if heavy charged material is dropped into the system, thus forming dent or cracking the wall or bottom refractory.
Improper manual charging can also lead to :
• Dangerous bridging situation where, the tangled pieces of scrap forms layer above & apart from the molten bath.
• If it is unnoticed by the operator, then it may lead to superheating of the bath, due to bridging , which may cause failure of furnace lining & run out.
• Manual charging also directly exposes metal splash to metal deck workers, which is very dangerous.
Remote charging furnaces:
Remote charging systems enhanced safety not only by allowing melt deck worker to be away from furnace during charging, but also reduce the chances of damage to the furnace lining & bridging situation.Construction :
Mitool make vibratory furnace charger consists of a vibrating feeder mounted on a moving trolley with a storage hopper mounted above the feeder. The metallic components like scrap, bales, pig iron, & other foundry returns are stored in the hopper. The hopper shape is specially designed to enable the bulky & irregular scrap pieces to be extracted without distortion.
The withdrawal of scrap from hopper is carried out by inbuilt vibrating feeder. The vibrating feeder design is such that, the material conveyed is spread out into individual pieces, as they flows towards the feeder discharge.
This technique brings about a accurate dispensing. The metallic components are dosed either into a weigh hopper or directly into the charge bucket. Weigh hopper is the one on which, weighing is done by means of provision of load cell indicator with digital weigh scale.
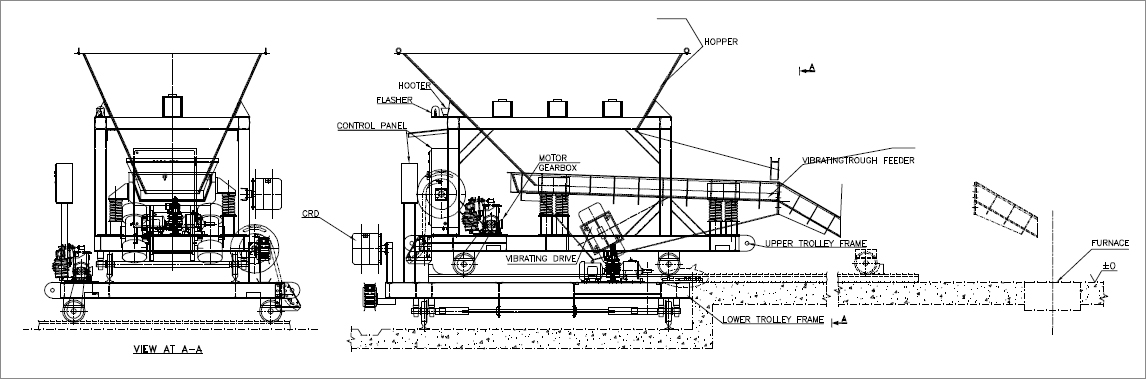
The charging car on the vibrating furnace charge consists of a discharge chute with complete vibratory furnace charging device. The discharge delivery end is inclined & formed of a rounded trough to bring about a good charge distribution and enable irregular, bulky pieces to be discharged. The feeder is driven by unbalanced vibratory motors. The vibration frequency can be altered by an AC Inverter, for regulating the feed velocity & also influencing the noise emission if required. The batch hopper as well as the charging feeder is built in sandwich construction which reduces the noise generated by contact between the charge materials & hopper walls or feeder tray. However, this does not eliminate the noise produced by contact between the charge pieces themselves.
Once the charge is prepared it is put into the storage hopper of the travelling charger. The charger drives from the loading point onto the furnace platform in front of the induction furnace. The furnace hood which is arranged in such a way that it can be fitted for charging and for pouring. The furnace lid itself hangs from a chain inside the hood. The hood is raised and the charging machine drives upto the charging point & then vibrating feeder is energized, the furnace filled and as the contents are melted down the furnace is kept full.